News
Meet the Team: Mark Chaplin, Machine Setter
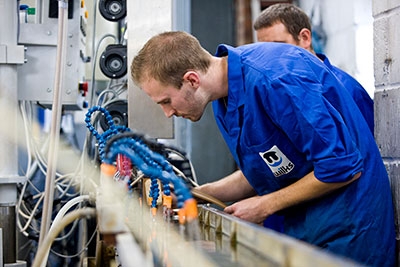
Step inside the Wilks factory and make your way onto the production floor with Mark Chaplin, Machine Setter.
Tell us about your background. What did you do before joining the Wilks team?
I joined Wilks after completing my A-levels. I started as a Coiler before progressing to my current role of Machine Setter.
How long have you worked here?
I started at Wilks in August 2005.
Tell us about a typical day – what does your job involve?
Here at Wilks, we manufacture a wide range of extrusions including marine fendering, shopfitting profiles and synthetic teak. As a Machine Setter, it’s my responsibility to make sure the machines are up and running correctly for every product.
This involves setting up each machine with the correct die and material and setting the speed and temperature. We have hundreds of different products and a whole range of synthetic teak colours, meaning everything has a slighting different “recipe”. I make sure each machine is running as efficiently as possible, quality checking the profiles as I go.
The factory floor is a busy place to be. I work with a team of Machine Setters and often have to be reactive and think on my feet. Cleaning down the machines is also another big part of my day, before getting them up and running for the next profile run.
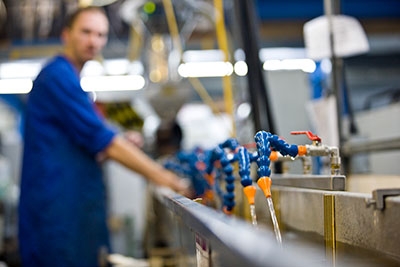
What do you enjoy most about your job?
I love when I run a machine as efficiently as possible, it’s great to know a job is well done.
What would you say your biggest achievement at Wilks has been so far?
Learning to manage materials and being able to plan the work for the entire factory floor.
How can you see your role developing in the future?
Now that we are part of Flexiteek International, I am looking forward to seeing a wide range of new profiles running in the factory.
What has been the weirdest thing you’ve had to do – or your strangest moment?
We mostly work with brown, black or white materials, so it made a nice change to work on a brightly coloured shopfitting profile a few years back for Pets at Home. The colour in question was hot pink, and it certainly livened up the factory floor!
What advice would you give to anyone wanting to do a similar role?
Starting as a Coiler helped me learn how the factory works. I got to see the production process first-hand, learning what each profile was gradually.
What do you do in your spare time?
I am kept busy managing my son’s football team outside of work and also enjoy playing snooker.